A real-time location system (RTLS) is an essential tool for businesses that want to improve manufacturing operations because it tracks and monitors the movement of critical assets, inventory, personnel, and machines, enabling manufacturers to optimize their production processes.
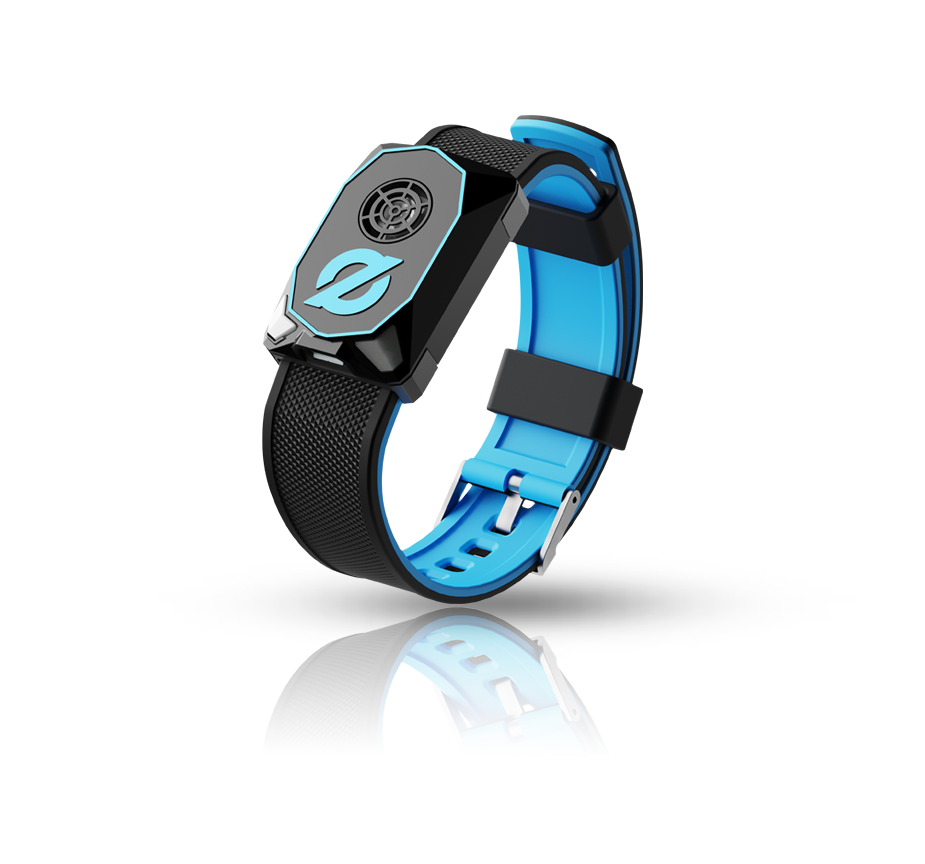
But what if we told you an RTLS could do more than just track the activity of materials throughout a facility?
Picture a positioning technology that could transform your manufacturing operations by digitally twining operations in real-time with 1.5mm 3D accuracy across an entire facility. The operational visibility achieved by this level of positioning accuracy would drastically increase efficiency gains, QA/QC, automation, and just-in-time process control. That’s where ZeroKey’s Quantum RTLS technology comes in. It offers the resolution required to improve manufacturing operations through high-fidelity digital twinning of everything from a singular workbench to complex production workflow tracking across your entire facility. This capability also enhances workplace training, allowing personnel to develop their skills in less time. These improvements enabled by digital transformation increase employee satisfaction, productivity, and loyalty, and reduce the skills gap within a company.
Quantum RTLS is a revolutionary millimeter-accurate location technology that leads the industry in accuracy by a factor of over 100. This highly advanced RTLS offers precise, real-time 3D tracking, and local to wide-area scalability. It’s a self-calibrating system with an open API and extensible plugin interfaces, low latency, and high update rates. By providing actionable insights and complete visibility into facility-wide operations, ZeroKey technology brings real-world workflows, material flows, and processes into the digital realm to modernize traditional industries globally.
Here are 10 Ways to Improve Manufacturing Operations with an RTLS
(click an option to navigate to each section)
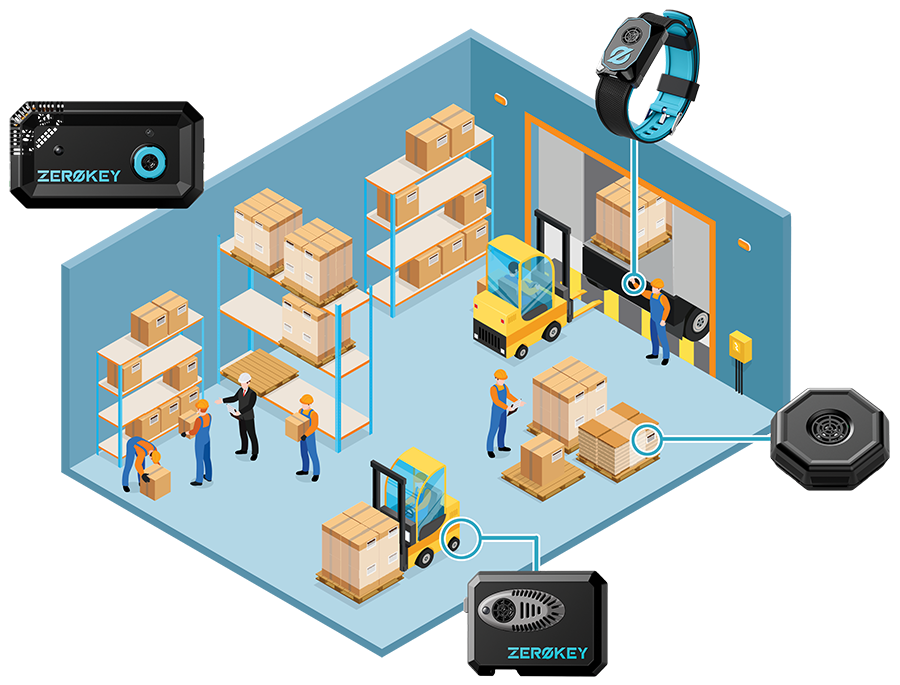
In typical manufacturing environments, numerous components operate in tandem. This can involve parts travelling along a conveyor belt, work orders transitioning between stations, or employees shifting between tasks – all contributing to a bustling factory environment. However, there are risks, such as the misplacement of parts, materials, or personnel. Movement within a facility may not always follow the most direct or efficient path. RTLS technology captures accurate location data in real-time, enabling manufacturers to uncover valuable insights that can be incorporated back into workflows for improved optimization of every process.
The wealth of information derived from tracking the movement and interaction of critical assets and workflows within a facility is exceptionally valuable. Real-time location data helps businesses improve manufacturing operations by enabling them to identify areas where optimization is possible. Analysis of motion histories can uncover deviations from standard procedures. Furthermore, timing data can be used to measure the duration of each production stage rather than relying on manual tracking by employees. Numerous practical applications arise from a comprehensive understanding of time and motion in manufacturing. As a result, modern factory management has significantly evolved from the “Taylorism” principles of the late 19th century.
With Quantum RTLS, operational data is transformed into valuable insights, resulting in unparalleled efficiency gains across your factory.
Widespread in manufacturing, scanning technologies like barcodes are frequently employed. In instances where the manufactured component cannot accommodate a barcode directly, it’s common for factories to implement procedures that advance work orders (featuring individual barcodes) concurrently with the production of the item at each stage.
Yet, scanning is an inherently manual and laborious task that is susceptible to human error. RTLS technology can significantly decrease these errors, enhancing the accuracy, efficiency, and flexibility of human-centric processes by providing automated, real-time updates instead of only providing updated information once an item is scanned.
With the help of Quantum RTLS, you can eliminate time-consuming scanning practices and automate updates.
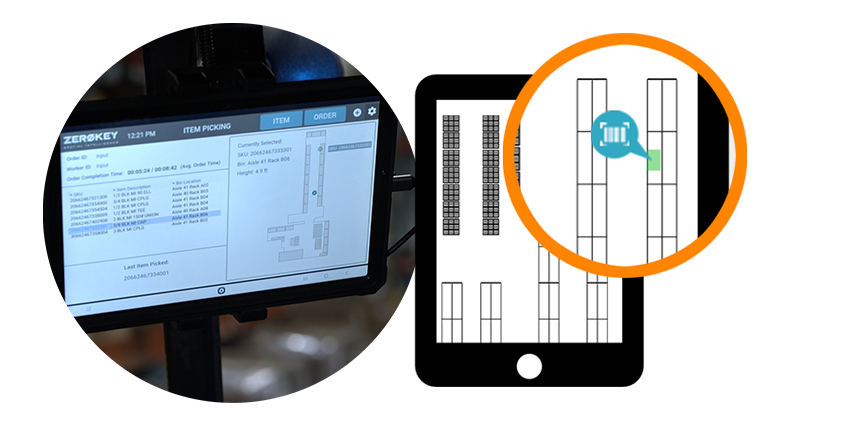
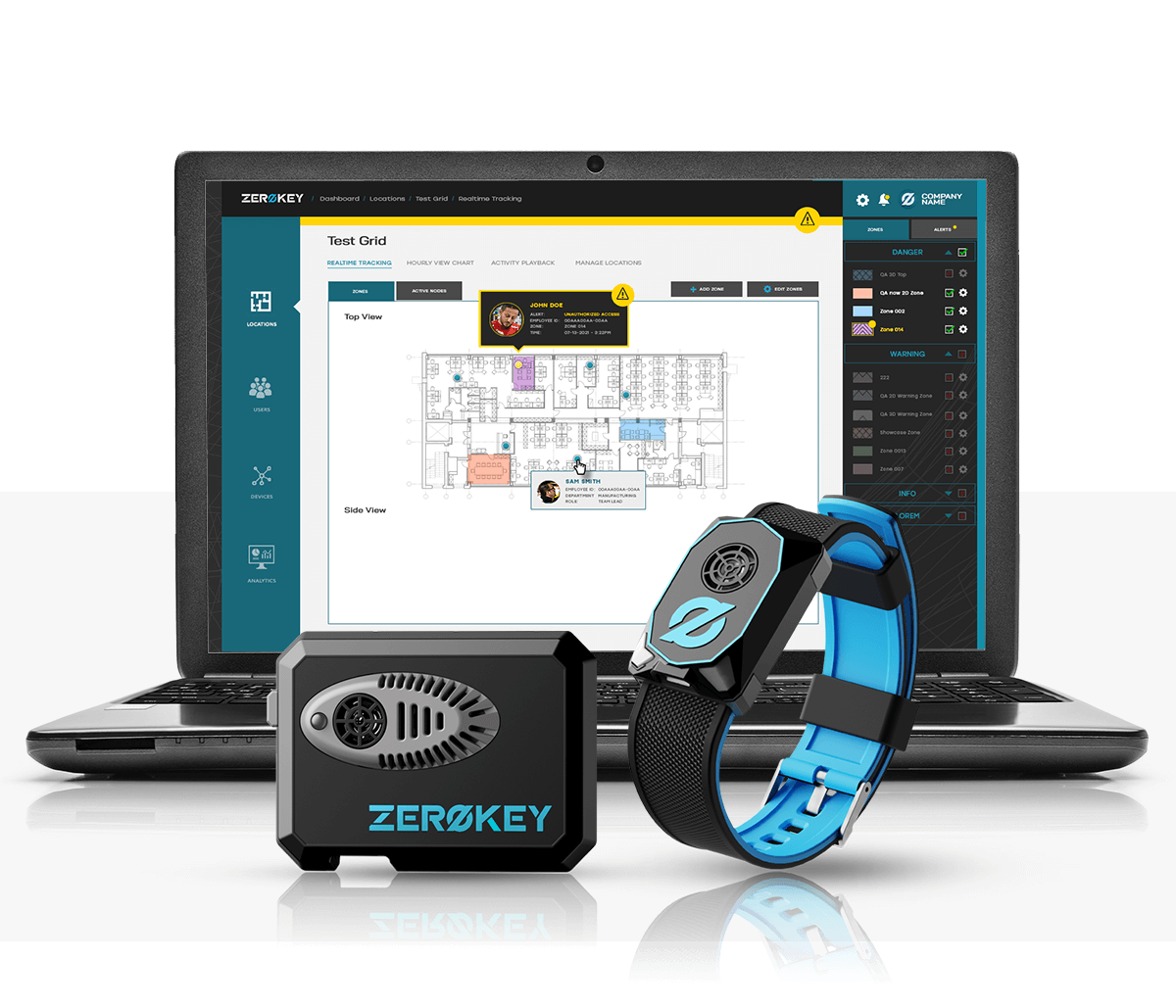
The topic of “last known contact” has garnered significant discussion recently. The crux of the matter: numerous contact tracing methods are currently employed in various workplaces, such as factories, to determine interactions between individuals in the event of possible infection. Several benefits arise from the use of an RTLS instead of mere proximity data, as RTLS technology captures the hyper-accurate data required to monitor human interactions, including timing, location, duration of the interaction and areas where individuals spent time between each encounter.
With Quantum RTLS, contact tracing at your workplace has never been easier or more accurate. The technology ensures worker safety and compliance by precisely capturing the real-time location, time, and length of each interaction.
Despite being a prominent concern for employee safety, businesses develop novel collision avoidance solutions each year. This innovation is due to the unfortunate reality that hazardous collisions continue to occur. In fact, workplace injuries amount to over $7 Billion annually in the United States alone, with collisions among the primary culprits.
Current safety practices businesses use to address this issue encompass vivid signage, audible warnings when vehicles or individuals are in motion, indoor traffic signals, deployable safety barriers, comprehensive training, and personal protective equipment for workers.
Quantum RTLS technology takes these strategies a step further by:
- Improving safety with real-time notification of operators during safety buffer breaches.
- Triggering instantaneous alerts when equipment unexpectedly leaves work area boundaries.
- Empowering operators to make safe decisions with real-time insight into staff whereabouts.
- Performing accurate, real-time collision detection and avoidance with cranes, forklifts, and personnel, thereby enabling the safe integration of humans and machines.
- Providing real-time data to guide the implementation of supplementary measures.
Make safety a top priority with ZeroKey’s world-leading location technology. Quantum RTLS reduces workplace accidents by giving businesses the data they need to develop and implement proactive collision avoidance measures.
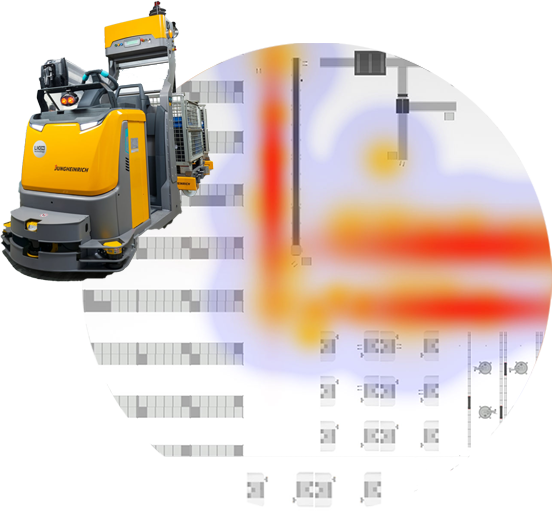
One crucial aspect of preventing collisions involves pinpointing where incidents are prone to occur. Creating heat maps from location histories helps businesses identify congested or dangerous zones. Recording the movement of forklifts, pallets, crewless vehicles, and employees enables clear visualization of shared spaces and the frequency of potential intersections. Analyzing this information offers valuable insights into whether it’s necessary to modify work schedules, alter operational procedures, or even redesign the workspace layout to enhance employee safety.
By using Quantum RTLS, which offers heat maps and movement analysis for enhanced safety, businesses can prevent site accidents before they happen.
The era of relying solely on physical barriers like walls, fenced enclosures, and locked doors to protect sensitive areas is over. Manufacturers can now establish geofenced zones and enhance safety by:
- Outlining the boundaries of a restricted area.
- Determining access levels for different individuals.
- Instantly notifying users when unsafe behavior is detected or when geofenced areas are breached.
Virtual perimeters may not prevent contractors or long-term workers from entering unauthorized zones, but they ensure that any breach is instantly and automatically reported to the worker and a supervisor.
RTLS technology can improve manufacturing operations by enabling the creation of dynamic restricted zones (geofences) that adapt to the movement of objects in real-time. Red zone geofencing replaces costly door readers by using real-time location information instead of badge scans. Moreover, leveraging location data is less invasive than using camera or vision-based systems, and RTLS’ allow geofenced zones to be limited to specific work areas.
Quantum RTLS instantly notifies users when unsafe behavior is detected or when geofenced areas are breached. The system creates safer workplaces through adaptive protection and real-time personnel alerts.
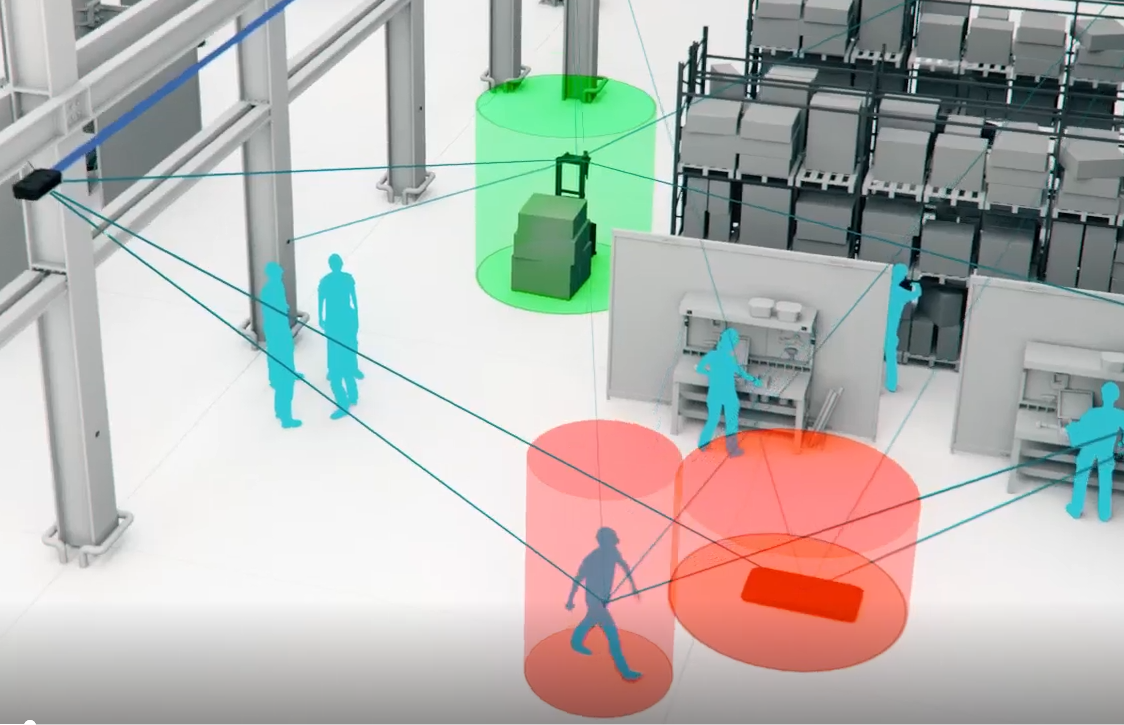
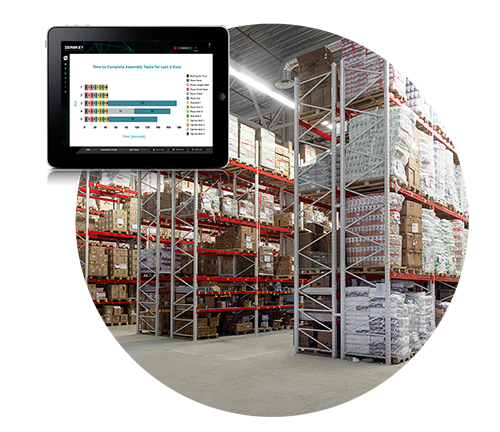
A significant advantage of RTLS technology is its ability to automate inventory management. Instead of scheduling operational downtime to search for essential tools, manually locating misplaced items, or re-scanning stationary materials, inventory control can now be self-governing and continuously up to date.
By automating these physical processes, inventory managers can monitor item circulation with minimal paperwork and generate tailored notifications for scenarios such as an item departing its designated zone, low stock levels, or when a worker achieves other performance benchmarks.
Improve manufacturing operations across your facility by streamlining inventory management processes, automating and customizing alerts, and enhancing overall efficiency with Quantum RTLS.
Monitoring the circulation of tools or rented equipment can pose significant challenges in manufacturing plants, where the exchange of countless items occurs daily. On the other hand, implementing RTLS technology to digitize, automate, and optimize facility-wide systems significantly alleviates these burdens, minimizes the risk of theft or misplacement, and boosts productivity.
For example, streamlining the checkout process can be achieved by accurately identifying a worker’s location and the designated storage spot for a crucial piece of equipment in real-time. The precise positioning accuracy RTLS’ offer allows for a seamless one-step procedure: simply acquiring the necessary item.
Quantum RTLS makes equipment checkout procedures more efficient by drastically reducing the paperwork required to track item rotation.
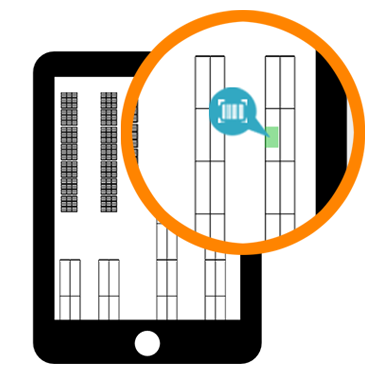
It is a common experience to reach for an object only to find it missing from its expected location. The misplaced item could be anything from car keys, a phone, a wallet, to a work order, forklift, or high-value asset. The result is the same: you must search for the missing item, retrace your steps, or inquire if someone else moved it. This leads to delays and increased risk for essential items.
RTLS technologyreduces this risk by enabling an instant virtual search for items equipped with sensors based on attributes like name, ID, category, or other characteristics. Instead of physically searching the factory floor, workers can input the relevant information on a mobile device and receive an accurate snapshot of the item’s location in real-time. Some RTLS solutions offer wayfinding capabilities, providing a guided path from the worker’s position to the desired item.
Quantum RTLS’ hyper-accurate positioning and digital twinning capabilities reduce downtime and productivity loss by enabling quick identification of objects that have been forgotten or lost.
Various equipment, such as pallets, safety gear, hand tools, bins, welding apparatuses, and even high-value items like forklifts, may stay dormant for extended periods, either due to misplacement, a collision, or limited use. RTLS technology offers a straightforward method for analyzing and optimizing the utilization of vehicles, AGVs, machinery, tools, and individual workstations.
Collecting data on the movement and interaction of the processes and equipment within your facility is a powerful strategy for optimizing available space, minimizing unnecessary acquisitions, and maintaining a lean operation. This approach also assists in pinpointing bottlenecks caused by equipment scarcity or other instances where additional purchases could result in enhanced productivity and increased revenue.
By gathering and analyzing the millimeter-accurate positioning data that Quantum RTLS provides, businesses can reduce costs by making better-informed and more timely decisions.
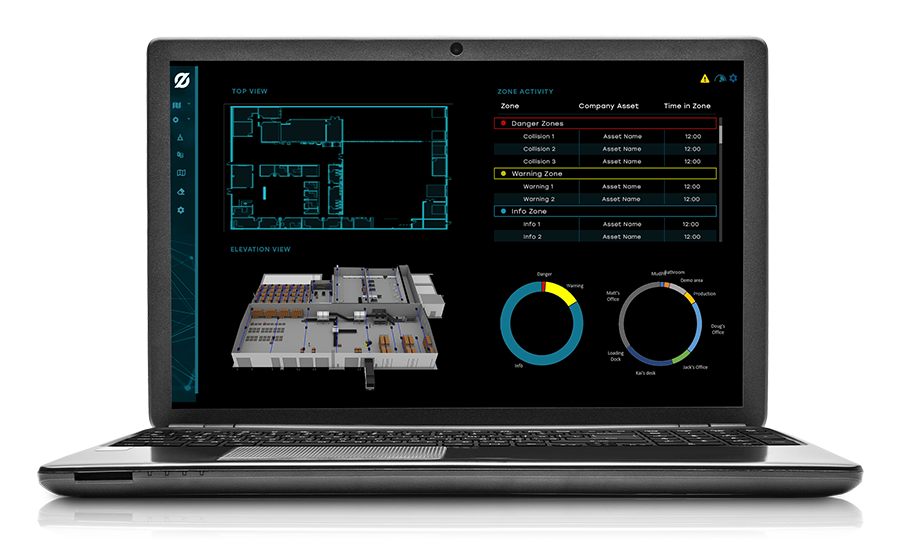
Quantum RTLS: Providing Unmatched Positioning Accuracy to Improve Manufacturing Operations
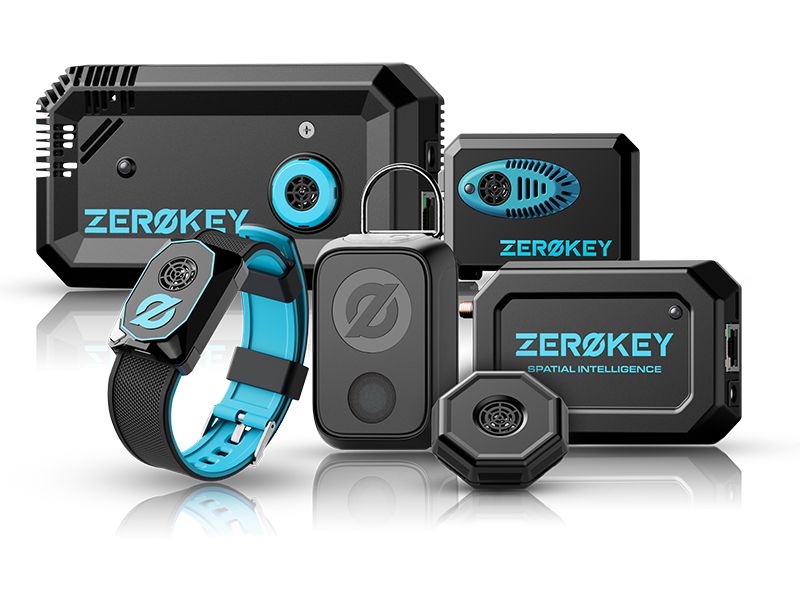
ZeroKey’s Quantum RTLS technology, a positioning system that relies on anchor and mobile nodes to capture location data for real-time 3D digital twinning of entire facilities, can be used for even the most precise applications due to its unparalleled accuracy. This includes assembly lines where millimeter-accurate tracking of worker hand positions is imperative for maximizing productivity and eliminating costly errors.
The system guides workers through kitting and assembly steps without manual input, streamlining factory efficiency and verifying production quality. It provides instant feedback when incorrect picks or missed steps occur, preventing supply chain quality issues. In addition, the system measures task cycle times in real-time to give businesses a comprehensive understanding of throughput.
Quantum RTLS can be scaled facility-wide, providing unlimited coverage for real-time monitoring of equipment, personnel, assets, and dynamic processes. This process digitization allows for increased automation, as it enables machines to predict and adapt to workers’ actions, ensuring improved safety and efficiency in any manufacturing environment.
Book a meeting with our team below to get started.