The Benefits of Empowering Frontline
Workers
with Digital Tools and Technologies
Digital transformation has become a buzzword in the business world, but what does it actually mean? At its core, digital transformation involves the integration of digital technology, including systems such as ZeroKey’s Quantum RTLS, into all areas of a business, resulting in fundamental changes to how it operates and delivers value to customers. While many companies focus on the high-level aspects of digital transformation, such as upgrading their IT systems and implementing new software, one area that is often overlooked is how to ensure new digital tools and resources are also empowering frontline workers within an organization.
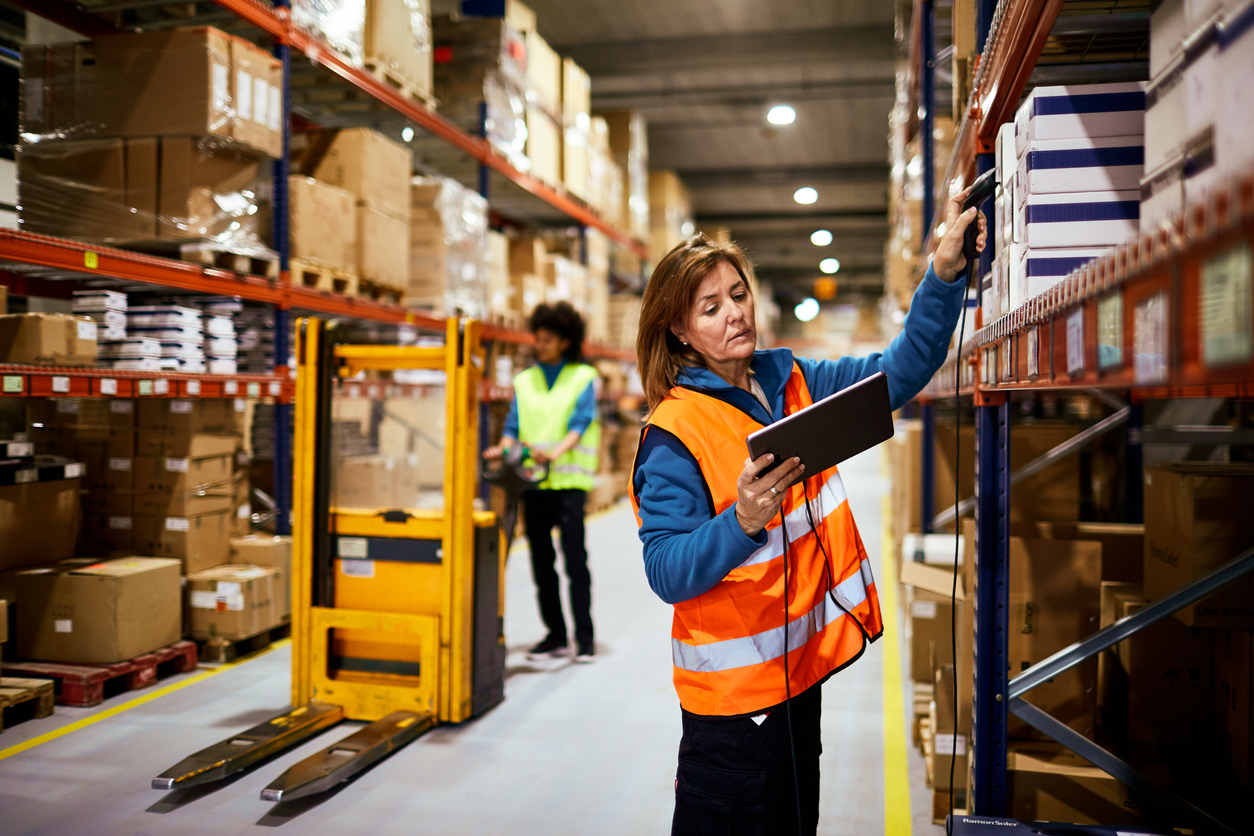
Frontline workers are the employees who are directly involved in the day-to-day operations of a business, such as customer service representatives, sales associates, and warehouse staff. These workers are often the face of a company, interacting directly with customers and playing a critical role in delivering products and services, but are typically most overlooked when it comes to digital transformation. Many companies assume that frontline workers are not tech-savvy and do not need advanced digital tools to do their jobs. However, this assumption is often incorrect. A new era of no-code technology means the ability to make meaningful changes to digital systems is no longer siloed to a specific team or department. After all, who better to design and build an operations dashboard or a workstation application than the end user?
Secondly, empowering frontline workers with digital tools can improve customer experience. By giving frontline workers access to customer data and insights, they can better understand customer needs and preferences and provide personalized service. Using an RTLS (Real-Time Location System) allows for continuous order status monitoring, giving frontline workers more granular updates to keep customers informed. System-wide process improvements enabled by RTLS technology increase order fulfillment speed while eliminating errors and mistakes that lead to incorrect order dispatching. Orders at risk of delays are flagged earlier, giving workers more time to notify the customer and implement countermeasures to rectify the situation. These supply chain and customer service improvements benefit both the customer and the business by increasing customer satisfaction and loyalty, and significantly heightening revenue and competitiveness.
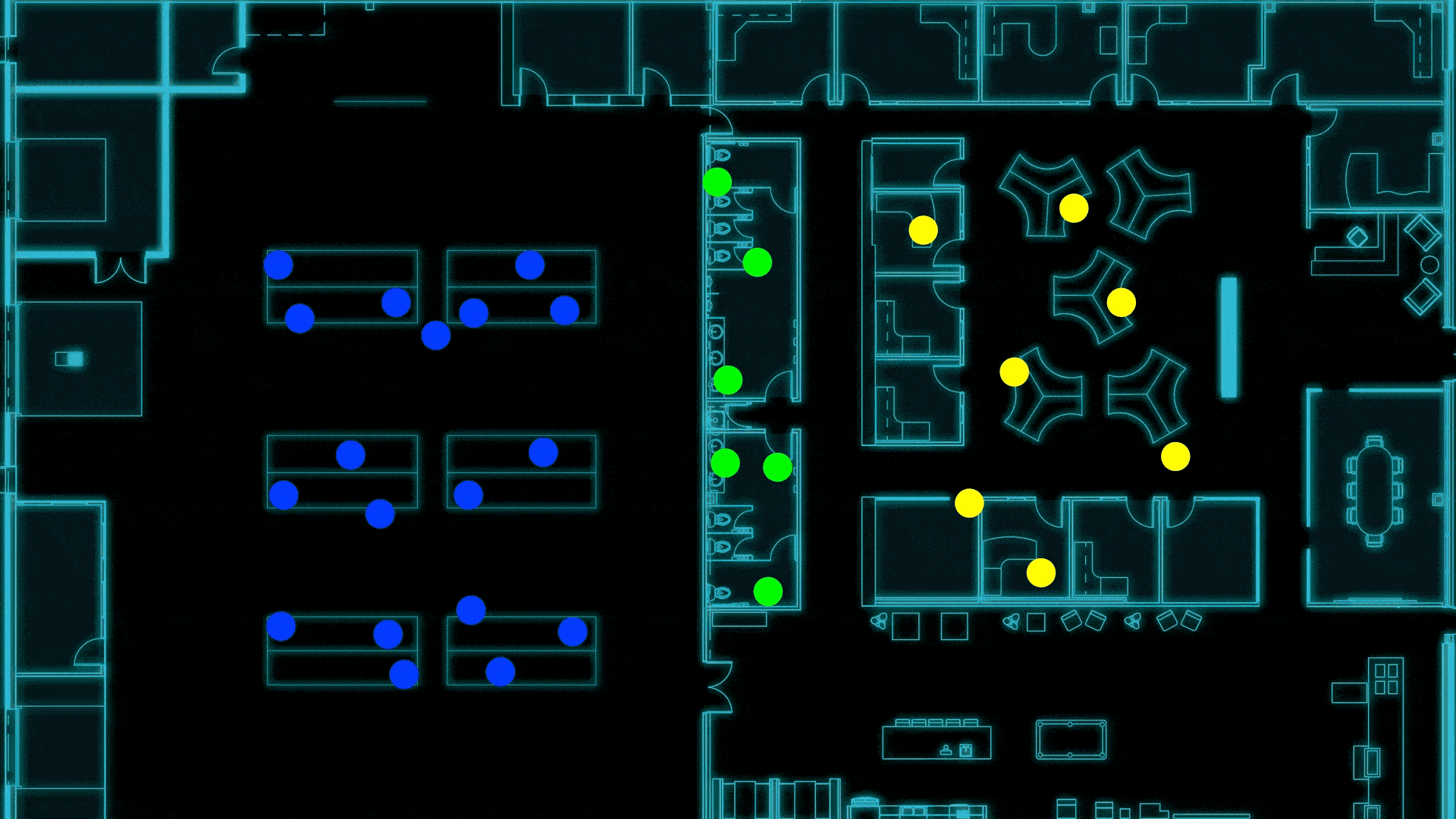
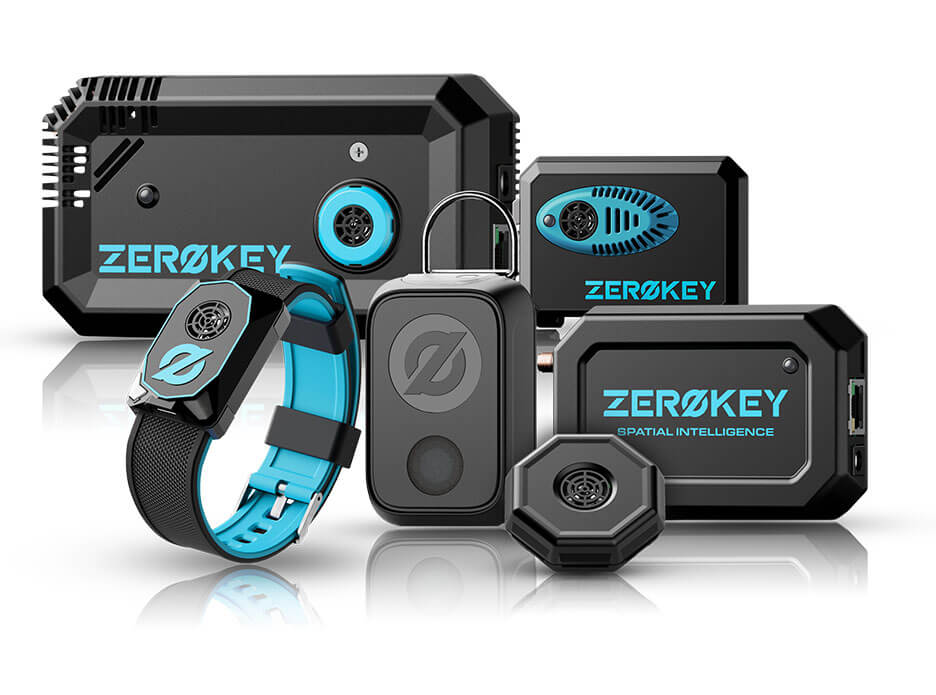
- Improving Supply Chain Operations with RTLS Technology – 10 ways that RTLS technology improves supply chain efficiency and resiliency.
- Indoor Positioning System Decision Guide – A detailed and updated guide to the strengths and weaknesses of current indoor positioning technologies, including Ultra-Wide Band (UWB), Bluetooth Low Energy (BLE), Proximity (including RFID), Vision and Ultrasonic (US). What are the pros and cons of different RTLS technology, and how do these impact your use case?
- A Guide to Deploying RTLS for Manufacturing – An expert guide to successfully deploying your first RTLS digital transformation project. Although this guide is manufacturing-focused, many of the same principles apply to other industries.
- RTLS Technology Overview – An in-depth look at the science behind positioning and what the future might hold for further RTLS developments.